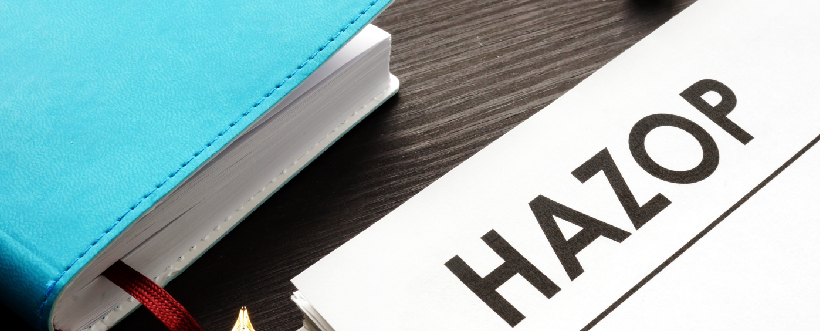
Breve introducción al método
El HAZOP, o también conocido como Análisis Funcional de Operatividad (AFO), es un método de identificación de riesgos de forma inductiva. Esta técnica nos sugiere que los accidentes son causados por una desviación en las variables del proceso con respecto a sus parámetros estándar de operacionalidad. Este análisis es realizado por un grupo multidisciplinar de trabajo en el que se abarcan varios sectores.
Este método es creado en 1963 inspirado por técnicas de análisis crítico. Se partía del planteamiento de un problema y su posterior estudio mediante la respuesta a preguntas relativas al ¿cómo?, ¿por qué?, ¿dónde?, ¿cuándo?, y ¿quién? Esta metodología se ha ido consolidando con el paso del tiempo, siendo de las más utilizadas en nuestros días para detectar riesgos, sobre todo en instalaciones de tipo industrial.
Fases de análisis del método HAZOP
- Definición del área de estudio y delimitación de la misma. Esta definición puede incluir una línea esquemática con subsistemas para su mejor estructuración, así podrán especificarse funciones propias de cada proceso susceptible de ser analizado.
- Identificación de los nudos. Seguimos desgranando el proceso y llegamos a la identificación de esos puntos clave de cada proceso, que van a su vez dentro de los subsistemas. La finalidad es encontrar la desviación que ha causado el problema para poder solucionarla desde la raíz. Un ejemplo sería, dentro de una instalación industrial, el chequeo del estado de una bomba que impulsa la separación de disolventes. Cada nudo será debidamente numerado para la comodidad de su estudio, ya que la técnica HAZOP será aplicada a cada uno de ellos. A través de variables como la presión, nivel, temperatura, etc., podremos detectar qué está causando el desvío.
- Definición de las desviaciones. Dependiendo del proceso que vayamos a someter a análisis necesitaremos establecer unas desviaciones específicas. Se establecerán, también, parámetros y palabras guías para facilitar el análisis.
- Organización por sesiones. La finalidad de este proceso es su ordenación a través de un formato que facilite y agilice la recogida de datos para su posterior análisis. En esta fase podremos consultar documentación como diagramas, manuales y fichas de especificaciones. Debemos tener en cuenta que para las plantas que incluyan procesos discontinuos es necesario hacer un estudio por cada uno de ellos para validarlo.
El informe final
Realmente este paso debería incluirse dentro del esquema de las fases, pero dada su importancia hemos querido hacer un extracto específico donde desglosaremos qué requerimientos tiene este documento:
- Esquemas simplificados
- Numeración de los nudos de cada subsistema.
- Registros de las sesiones con indicación de las fechas de realización.
- Fichas del equipo de trabajo con especificaciones de su labor.
- Análisis de los resultados obtenidos.
- Clasificación de las consecuencias para nuestra organización.
- Conclusiones y posibles soluciones. Debemos tener en cuenta la repercusión de la solución de un nudo al resto del proceso. Establecer si es un hecho que se repite o que se ha dado de forma aislada.
- Podremos realizar una lista donde se recojan todos los problemas especificando su nivel de urgencia e importancia para procesos futuros.
Ámbito de aplicación y recursos necesarios
Las instalaciones con procesos de relativa complejidad, y los sectores de almacenamiento que contienen equipos de regulación o de diversidad de tipos de trasiego, son los ámbitos de aplicación más comunes para el HAZOP.
Es recomendable implantar este sistema en nuevas aperturas para hacer un checklist de posibles fallos en el diseño, en la construcción, en torno a la funcionalidad y a la instalación, etc.
Este método es realizado en conjunto por un equipo de trabajo dirigido por un coordinador. Deberá estar compuesto por:
Responsable de proceso.
Encargado de la operación de la planta.
Responsable de seguridad.
Responsable del mantenimiento.
El propio coordinador.
Técnicos especialistas en otras áreas disponibles para su consulta.
Si la planta está en fase de diseño y construcción, debemos sumarle a este equipo un responsable de diseño, uno de proyecto y el futuro responsable de la puesta en marcha.
Todos ellos deben ser profesionales expertos en su campo y que conozcan las instalaciones a la perfección. La proactividad también se valorará de forma muy positiva a la hora de formar parte de este equipo.
Software para la gestión de riesgos operacionales ERM
El método HAZOP requiere una buena coordinación entre equipos para poder ser efectivo a la hora de solucionar problemas de forma rápida y efectiva. En GRCTools, tenemos la solución a tu medida para la implementación de este sistema en tu organización. Gracias a un software de gestión de riesgos operacionales, la organización podrá tener bajo control los riesgos de forma sencilla y completa.
- Gestión de Riesgos de Terceros: Cumplimiento Normativo y Responsabilidad Corporativa
- Prevención de riesgos de ciberseguridad: Tácticas efectivas
- Cumplimiento en la Cadena de Suministro: Riesgos y Controles Eficaces
- ¡No te pierdas el ESG Innova Group Summit IV!
- ¿Cuáles son los elementos que desarrollan los componentes del modelo de capacidades de GRC?
¿Desea saber más?
Entradas relacionadas
Gestión de Riesgos de Terceros: Cumplimiento Normativo y Responsabilidad Corporativa
La Gestión de Riesgos de Terceros se refiere al proceso de identificación, evaluación y mitigación de los...